SAN DIEGO, Calif. (USNI News) – If a part breaks on a ship or submarine sailing in a conflict zone or moored at its homeport, the fix just might be done with a portable welder or a mobile workshop set up on the pier in an unconventional way, using an innovative technology known as “cold spray.”
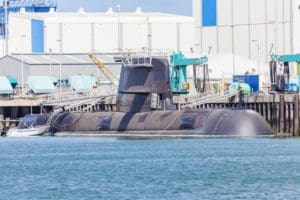
Fleet Fixes with Cold Spray Technology
Cold spray uses a highly-pressurized gas that fires heated metal powder at supersonic speed to lay metal onto a surface. It’s not cold, per se, but at 800 degrees Celsius or so is far cooler than traditional “hot” welding.
The technology uses a process called high deposition rate additive manufacturing. It uses various types of powders – ranging from aluminum to titanium as well as specialty powders – for hard coatings as well as customized repairs including aircraft panel fasteners, damaged pipes and shafts, corroded impellers, joint leaks and valve actuators, according to the company. It can replace worn metal coatings with metal that’s at least as strong and hard as the original coating, officials say.
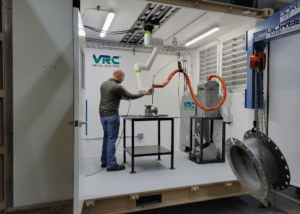
Cold-spray technology isn’t new – it was developed in Russia in the 1980s – but has become a growth industry garnering great interest and use by the military services grappling with parts shortages, clogged supply lines and demands for rapid-repair capabilities for deployed forces.
“[Cold spray] is one that we are really going after,” Rear Adm. Jason Lloyd, U.S. Naval Sea Systems Command’s chief engineer, said last week during the American Society of Naval Engineers’ annual Fleet Maintenance & Modernization Symposium.
The Navy has already seen months shaved off specific ship repairs using the technology, but the equipment can be prohibitively expensive. Now the Navy is developing a unique partnership with a company that’s developed smaller portable and deployable cold-spray systems that can be rapidly fielded and deployed.
“It’s a real advantage for getting after some repairs – not all – but it gives shipyards and local repair the option of using a different repair method,” said Lloyd, who also serves as NAVSEA’s deputy commander for ship design, integration and naval engineering (SEA-05). The Navy first used cold spray in 2019 at Norfolk Naval Shipyard, Va., and “the shipyards have been using them quite a bit,” he said.
To defray the high cost of the equipment, the Navy is investigating using the repair capability as a service provided by a commercial partner. The as-a-service arrangement might provide an entry point for private yards and smaller businesses that otherwise couldn’t afford the investment.
“This is going to take a monumental will to get where we need to go,” he said. “We have near-term competitors that we have not had in my time in the Navy.”
The Navy has partnered with VRC Metal Systems, a Box Elder, S.D.-based company that specializes in cold-spray technology, to create “pop-up” production cells within 90 days, which will be located near ports. The company will use equipment leased by the Navy to do repairs in three weeks or less – and at no cost to the customer.