Replacing worn-out or damaged products presents a variety of challenges for any company. Extending product life cycle stages as much as possible is the goal of many an Operations Director or COO.
The cost of replacement can be prohibitive as well as unexpected when a part breaks down. Plus, replacing equipment often means significant downtime for your production line, repair services, or other industrial applications.
VRC Metal Systems drives its service with these challenges at heart. Our custom-designed cold spray technology solutions help your organization remain nimble, prolong product life cycle stages and function, and increase your operational “up-time.”
Contact us today to begin collaborating on your next repair project, and preserve the life of your equipment indefinitely with cold spray technology.
What are the benefits of cold spray repairs over other methods?
Cold spray coating works by shooting pressurized gas and small particles of coating material through a nozzle at a very high velocity. The high kinetic energy of the accelerated particles deforms and activates on the impact the surfaces enough to bond molecularly with a substrate material.
Cold spray technology differs from thermal coating methods in that both the coating and the substrate heat up, but just enough to bond tightly without becoming molten.
During the spraying process, the additive and substrate particles “plasticize,” meaning they mold around each other almost as if they were warm plastic, and the high-velocity impact blasts away surface oxides, allowing a true metallurgical bond to form between impacting particles.
Some of the advantages to a cold spray coating process over a thermal one are:
- Heat-sensitive alloy compatibility
- Low thermal stress
- It does not require an inert environment (you can apply cold spray coatings in a variety of settings.)
- Can process metals prone to cracking in thermal coating applications
- Reduction or elimination of oxidation in an open environment
- Choose high pressure for depositing high strength metals (like steel and titanium alloys) and to achieve the best properties (even for softer materials like copper and aluminum)
- 3D printing capabilities as near-net-shapes
- Formation of dense, strong bonds with high rates of deposition
- Potentially dramatic cost savings over thermal coating methods
- Nimble application–you may be able to repair equipment with cold spray technology without equipment removal from your line, or component removal from the product
- Low material waste–with minimal masking and high deposition efficiencies
- Energy-efficient technology, which may lower your carbon footprint
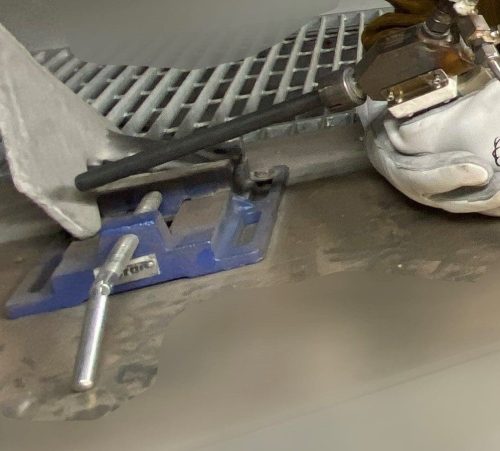
Cold spray can be used again and again on the same bond
While repeated welding can increase the risk of corrosion in some materials, cold spray technology does not share this risk. In effect, cold spray remains an effective repair method no matter how many times you coat the same surface.
Remember, cold spray bonds do not shrink from solidification or sensitize the substrate as other thermal coating processes may. The resilience of CS coating is superior in many applications.
Also, cold spray systems can adapt to just about any working space and do not need specialized environments in which to be effective. Your cold spray technology goes where you need it to, and bonds to surfaces reliably and repeatedly.
Industrial applications for cold-spray repairs
B-1 aircraft hydraulic lines often chafe during use. These lines are made of titanium, a lightweight and formable metal that is necessary to bend around the tight spaces inside the aircraft. However, titanium is also vulnerable to chafing wear, surface scratches, and other “dings” that can negatively impact the line’s safety and function.
These lines (notoriously) often need replacing, which gets expensive and time-consuming quickly, making it one of the most common and costly maintenance items on the aircraft. Cold spray technology has been shown to increase the product life cycle stages in these titanium hydraulic lines by laying down a protective titanium coating in high-chafe areas to extend their service life.
Inspectors can discern between the coating and the actual tube by the varying degrees of reflectivity in the tubing material versus the cold spray coating.
Safety inspectors can also use ultrasonic thickness inspection to determine when chafing through the protective layer on the hose surface threatens to expose the tube itself. When the protective layer wears thin, repeated CS coating layers can be applied to reinforce the chafe area and prolong the titanium tube’s life indefinitely.
CS coating over replacement saves time and money each time a new coating is applied
Further, using helium as the propellant in this application prevents a brittle crust or alpha case from forming around the coated area of the line.
Cold spray technology can also extend the product life cycle stages of parts of equipment made of titanium, magnesium, and related alloys.
The ability to apply cold spray coatings without completely disassembling machinery or production lines makes this technology an obvious repair choice in many instances.
Think of cold spray coatings for finished product repair (aircraft engines, automobiles) as well as for the machines that create them (coating, protecting, repairing production line equipment.)
The automotive industry also continues to expand its use of cold spray technology by coating synchronizers and pistons to extend their lives. The auto-body industry also uses cold spray more and more for bonding and protective coatings.
More repair possibilities for cold spray technology
Several other industrial applications for cold spray coatings look promising and can provide a foundation for expanding cold spray’s use.
Cold spray helps protect the turbines in jet engines by repairing small flaws in superalloy components, that if left untreated could become a critical failure down the road. This technology also lengthens the part life cycle in older naval ships and their components.
In the medical industry, cold spray can provide antimicrobial copper coatings to create self-disinfecting surfaces that prevent the formation of biofilms to help reduce hospital-acquired infection rates and slow the spread of other contagious bacteria and viruses from common touch surfaces.
Partner with VRC Metal Systems to increase your product life cycle stages VRC Metal Systems leads the industry in customized cold spray applications. Whether your goal is to repair, protect, or create in your operation, the team at VRC Metal Systems can build or curate the right equipment for the job.
Our intimate and evolving experience with a wide variety of cold spray applications makes us adept collaborators in developing new cold spray solutions. We work with and for a wide range of industries, and our cold spray innovations evolve continuously.
Contact us today, and we’ll get in touch to discuss your needs and provide the cold spray technology strategy and implementation you require.